PetroScale – A TRUSTED PARTNER FOR PRACTICAL RESERVOIR SOLUTIONS
Case Studies
Reservoir Stewardship: PetroScale is your trusted independent and objective adviser through the strategic development of practical workflows, informing better decisions in field execution to achieve leading results.
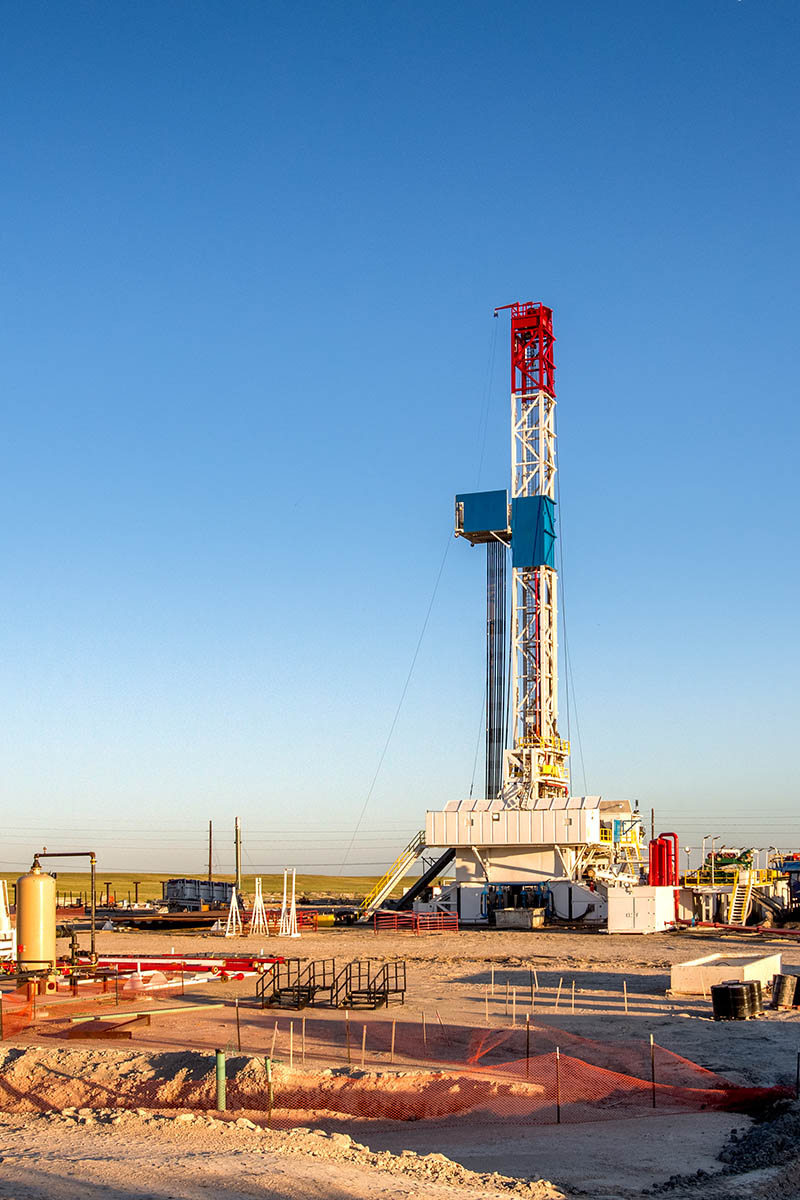
Permian Basin
Petroscale improved a client’s operational efficiency by utilizing drilling data, LWD logs, and cuttings geochemical data to calculate Bulk Rock Composition (BRC) of the reservoir. Knowing the BRC allowed perforation clusters to be modified from the typical geometric spacing to improve fracturing operations. Our testing of treatment fluids identified an incompatible fracturing fluid additive mistakenly delivered to the wellsite so we prevented creation of a downhole emulsion.
Our objective was to improve the understanding of lateral variability in the target formation using drilling logs, cuttings and LWD-GR logs. These data presented little to no operational risk, while at the same time provided information about the reservoir along the horizontal. We used machine learning algorithms and combined these data to generate new interpretations not available with existing approaches. Our methodology makes use of LWD logs, drilling data, cuttings geochemistry, and off-set (nearby) vertical pilots wells with full suite logs. We then applied machine learning, multivariate statistics to calculate Bulk Rock Composition (BRC). This defines the major rock-forming minerals at LWD-log-scale, which was tied into vertical wells within the studied area, formation, and basin. These data were then further calibrated to measured mineralogy on cuttings where available.
We performed the above workflow (on Pilot and Horizontals) in two step-out exploratory areas in the Midland and Delaware Basins. The rock composition information proved useful throughout the fracturing treatment, and results from each stage, pumping diagnostics, were also used as the basis for electing to skip certain intervals deemed problematic (from a pressure pumping “break-down” standpoint). Per stage fracturing success rate increased to greater than 90%, where (1) calculated rock composition and (2) fracture gradient were used together in the decision-making process.
It is well established that laterals frequently encounter stages that reach maximum pumping pressure and result in deviation from the planned design. Rock composition information (BRC) along the horizontal can assist in understanding the difficulty in portions of the lateral. This information can also assist with pre-frac planning, placement of stages, de-risking geohazards, and identifying “like-” versus “heterogenous-” rock. Log-scale mineralogy tied to measured geochemistry of cuttings has the potential to improve pumping success rate as well as stage placement in multiple reservoir types. Any reduction of stage screen-outs improves operational efficiency and improves individual well economics at minimal cost.
Weald Basin, UK
Operator Objectives: Reduce the risk associated with field development by accurately characterizing target formations (Portland Sandstone and Kimmeridge Lime) to better understand the oil resource and the oil source.
- In the Portland, work included defining the rock-matrix mineralogy and the oil/water contact.
- In the Kimmeridge Lime, an assessment of the formation was performed as well as determining OIP for targeted intervals.
Our value to the client:
- Compiling existing customer data for review and evaluation
- Amending data set where needed
- Starting with uncorrelated logs, we performed the required analysis to develop the mineral model to describe the reservoir; standard analytical techniques (XRF and XRD) used to develop the model.
- Partnered with the client to develop a methodology to geo-steer the horizontal through the upper section (oil leg) of the Portland in the next well.
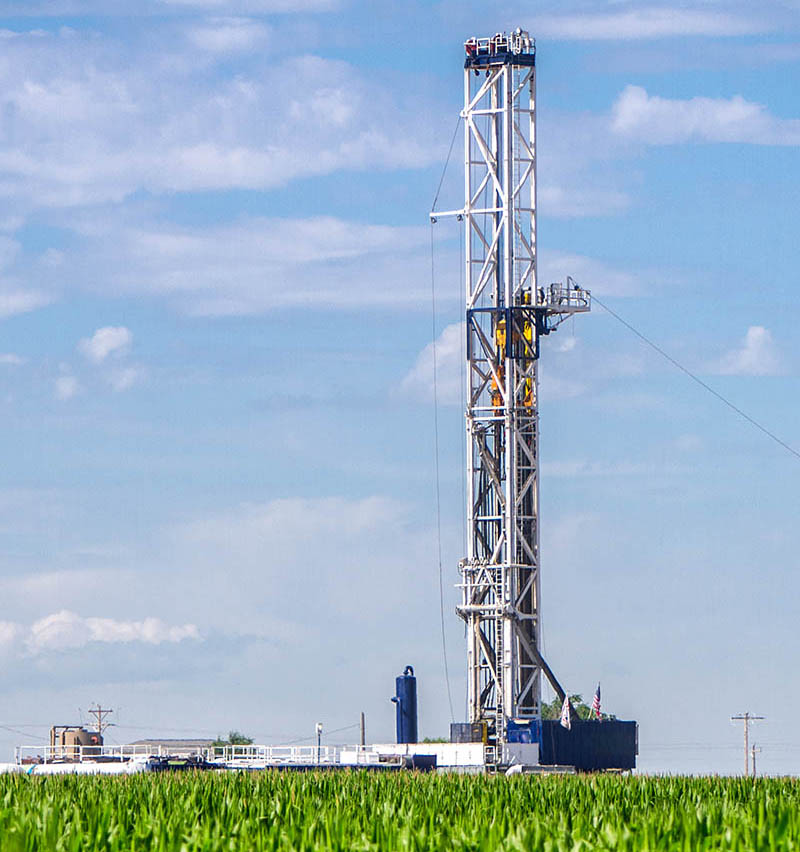
Common Failures
Common Failures with Frac Jobs Not Meeting Performance Expectations
Approximately 1 in 5 (20%) of the frac jobs performed did not meet performance expectations based on a comprehensive industry survey by Welling.
The most common failures or shortcomings in frac jobs not meeting expectations involved the lack of understanding of the reservoir properties to successfully design a completion that optimizes production. This involves reservoir characterization and the integration of multiple reservoir attributes from laboratory analysis to engineering.
With a significant portion of drilling costs dedicated to completions and the eventual performance of the reservoir at stake, the is simply too much risk in not implementing a completion strategy that is tailored to your reservoir’s characteristics. PetroScale will add value to your project and could be the difference in a successful return on investment.
Source: Welling & Company Worldwide Hydraulic Fracturing Survey
- Failure to Understand Subsurface Reservoir – 55%
- Inexperienced Crew / Human Error – 18%
- Downhole Equipment / Tools – 14%
- Poor Frac Design – 14%
- Subsurface Equipment – 14%
- Poor Frac Fluid Design – 13%
- Poor Reservoir Quality – 10%
- Well Placement / Integrity – 5%
PetroScale helps clients mitigate their risk and exposure while lowering costs and increasing reservoir performance.
Contact PetroScale, Today.
Please feel free to contact us. We look forward to hearing from you.